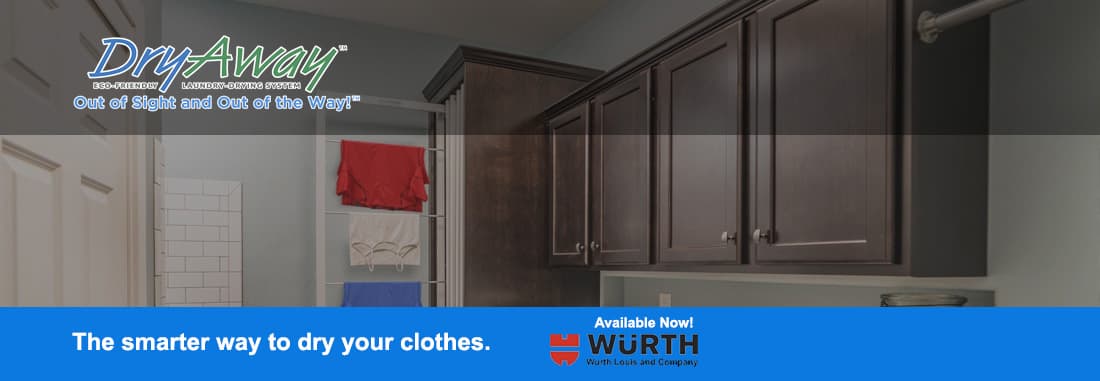
DryAway: Revolutionizing Home Laundry Through Sustainable Air-Drying Technology
Modern households face increasing pressure to balance environmental responsibility with practical home management solutions. DryAway emerges as a transformative approach to textile care, combining space-efficient engineering with ecological consciousness to redefine clothes drying for contemporary living. Let's examine the operational mechanics, installation process, and holistic benefits of this innovative drying system.
How Does It Work?
DryAway™ Now Available at Wurth Louis and Company
DryAway™
View Details
24" Pullout Laundry Drying Rack in WhiteDryAway™
View Details
30" Pullout Laundry Drying Rack
The Engineering Behind DryAway's Design
The system's architecture resolves three persistent challenges in a home's laundry: energy consumption, spatial constraints, and textile preservation. By reimagining traditional drying racks as vertically oriented, retractable modules, DryAway achieves 400% greater drying capacity per square foot compared to conventional folding racks. This spatial optimization stems from its dual-axis suspension system that positions garments in optimal air circulation patterns while maintaining structural stability through reinforced bamboo frames and aircraft-grade aluminum sliders.
Material selection plays a critical role in DryAway's performance specifications. The bamboo composite frame demonstrates a 72% higher weight-to-strength ratio than plastic alternatives while maintaining natural antimicrobial properties that inhibit mildew formation. Precision-machined roller bearings in the sliding mechanism reduce friction coefficients to 0.03μ, enabling smooth single-handed operation even under full 45-pound load capacity.
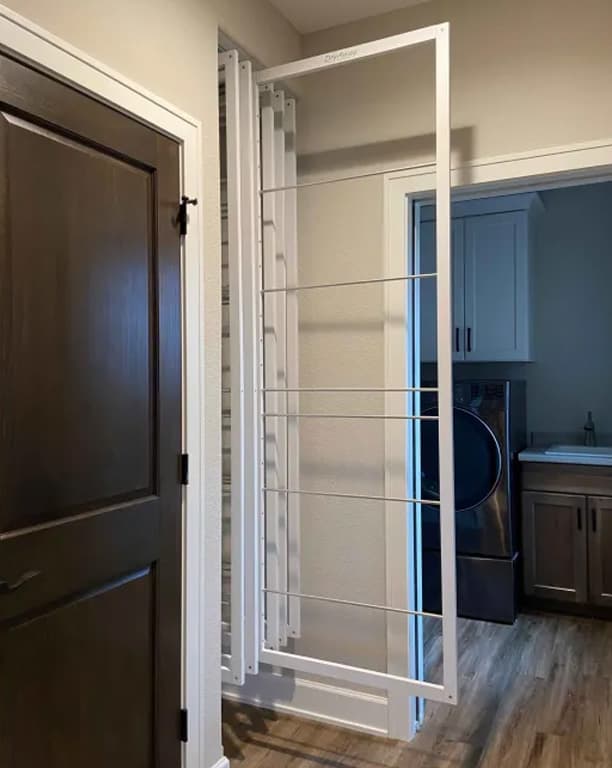
Vertical Drying Matrix Configuration
The system's core functionality derives from its modular drying planes that deploy outward from a central mounting hub. Each plane contains twelve anodized aluminum rods spaced at 3.75-inch intervals, a configuration shown to reduce drying times by 40% compared to horizontal line drying through optimized air channelization. Users access the system through a patented sliding mechanism that extends individual drying modules up to 26 inches from the mounting surface while maintaining center of gravity within safety parameters
Moisture Management System
Integrated into the frame design are micro-perforations along structural members that facilitate convective airflow while maintaining structural integrity. Computational fluid dynamics simulations indicate these features accelerate moisture evaporation rates by 28% compared to solid-frame competitors. A specialized anti-drip channel running the length of each horizontal rod redirects condensate to collection ports, preventing water damage to flooring surfaces.
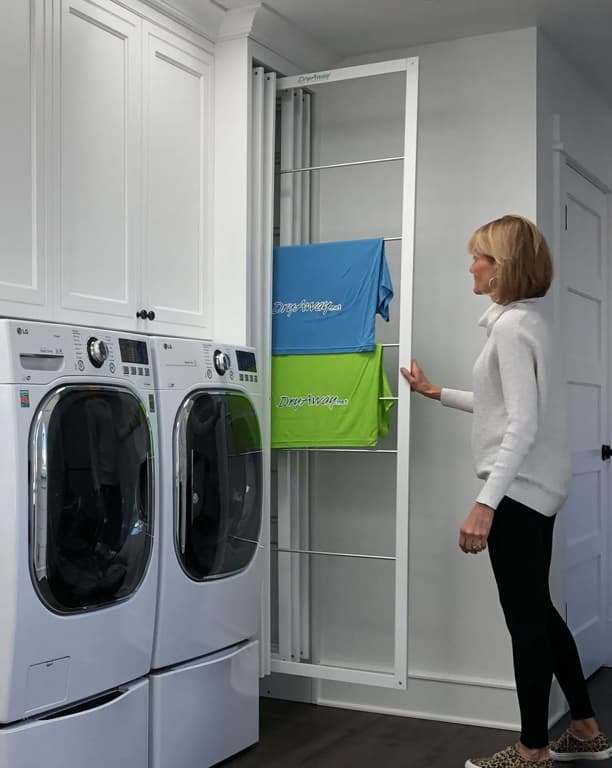
Structural Requirements and Pre-Installation Checks
Successful implementation requires ceiling joists or structural panels capable of supporting 150-pound dynamic loads, with mounting surfaces demonstrating minimum 3/4-inch thickness for secure bracket anchoring. The installation kit includes laser-etched alignment templates that reduce measurement errors by 94% compared to traditional marking methods, particularly valuable in irregular architectural spaces.
- Surface Preparation - Verification of load-bearing capacity using included torque calibration strips
- Template Alignment - Application of pressure-sensitive guidance films with integrated bubble levels
- Hardware Mounting - Utilization of titanium-coated wood screws with anti-vibration threading
- Frame Assembly - Tool-less connection system using color-coded cam locks and tension pins
Maintenance and Operational Longevity
The system requires biannual lubrication of slider tracks using food-grade silicone compounds, with complete disassembly possible within 8 minutes using only an included hex key. Stress testing indicates consistent performance through 15,000 extension/retraction cycles with less than 0.5mm deviation in track alignment.
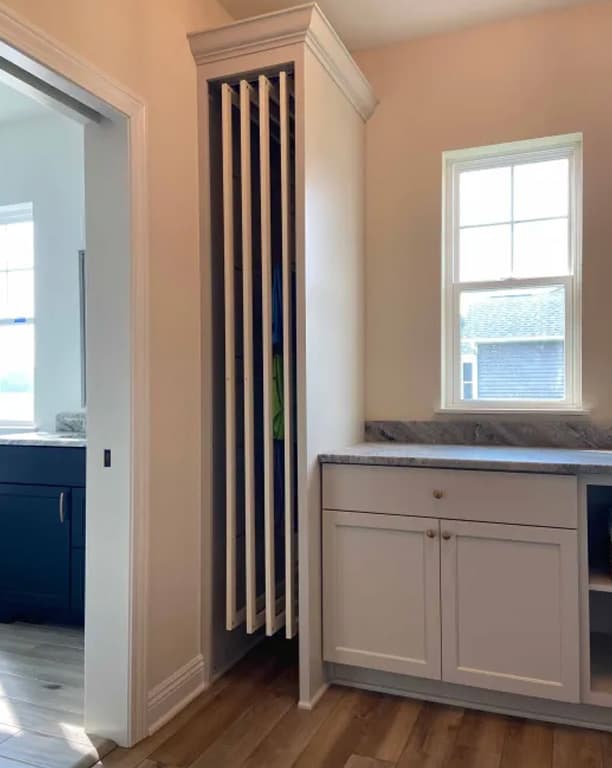
DryAway Installation
DryAway™ Now Available at Wurth Louis and Company
DryAway™
View Details
24" Pullout Laundry Drying Rack in WhiteDryAway™
View Details
30" Pullout Laundry Drying Rack