Cantek EM12 End Matcher
This item may incur additional shipping costs and lead times.
Product Details
The Cantek EM12 End Matcher is specially designed for machining tongue and groove (with or without bevels) on hardwood flooring and wall/ceiling paneling up to 12” wide. Its compact design with continuous through feed system allows for maximum output in a small space. Equipped with a user-friendly touch screen interface allow for simple operation with excellent performance and error diagnostics. The dual counter-rotating cutterheads produce both the tongue and groove simultaneously ensuring a perfect match. The anti-tear-out blocks and counter rotation of the heads ensure optimum cut quality without chipping or blowout. The insert style segmented cutterheads can be adjusted according to your desired tongue / groove thickness and can perform a micro-bevel or not. The variable speed infeed conveyor, variable feed speed, and variable cross-cutting speed allow the operator full control according to the type and size of material being run. The innovative clamps allow for simultaneous top and side clamping to ensure pieces are perfectly square for consistent end matching results.
Why Cantek EM12 End Matcher?
- Capable of processing end matching on flooring or paneling up to 12" wide x 1.38" thick.
- The Through-feed system allows the tongue and groove to be cut simultaneously on the tail of one board and the leading edge of the next board.
- Powerful dual 10HP cutterhead motors allow maximum cutting rate no matter the wood's width, thickness, or species.
- Stackable insert knife cutterheads allow for perfect matching of tongue and groove thickness.
- Variable cross-cutting feed speed and anti-tear-out blocks produce optimum finish quality on tongue and groove.
- Minimal floor space required with through feed design.
- A user-friendly PLC control touch screen can keep track of total linear feet cut as well as piece count.
- Production capacity of 77 lineal feet per minute based on an average of 6.5' board.
Key Advantages
- Variable speed through-feed system is controlled by frequency inverter.
- Powered top urethane rolls and spring-loaded bed rollers feed the material into position for processing.
- Pneumatic side pressure system ensures the material is held square against the fence.
- Capable of processing material as short as 12" to an unlimited length.
- Cutterheads are stacked and fully adjustable with replaceable and rotatable insert knives.
- Cutterheads are equipped with a removable micro-bevel insert cutter section for bevel or square flooring/paneling.
- 118" powered infeed table with angled rolls ensure material is fed up against the infeed fence.
- 87" outfeed slide table allows the board to slide out of the way while the next board comes through to be processed, resulting in continuous production.
- Chrome table ensures maximum wear resistance.
- Complete safety and noise reduction enclosure.
- The added feature of an inverter-controlled infeed conveyor allows you to slow the infeed speed when dealing with heavy boards.
Full Machine View & General Operation
The material travels from right to left. Each board is placed on the powered infeed conveyor and transferred automatically into the machine. The material will then be clamped and process the tongue on the right side and then groove on the left side. The material will exit the machine on the left and go on to a sliding table.
User-Friendly Touch Screen Control
The touch screen interface was designed with the operator in mind. It controls the machine's operation and keeps track of the number of pieces machined, total length machined, and more. These totals can be reset for each job if desired. Here you can also adjust the feed speed cutting speed of the machine.
118″ Powered Infeed Conveyor
The powered infeed conveyor brings material into the machine automatically. The rolls are slightly angled to bring material up against the fence. An inverter from the control panel adjusts the infeed conveyor speed to allow the operator to adjust the speed if necessary. For example, they may slow down the conveyor when feeding wide and long boards
Tongue and Groove Insert Knife Cutterheads
The tongue and groove cutters use insert knives that can be rotated for a fresh cutting edge. The cutterheads come in three sections which allows you to adjust the thickness of the groove and tongue. The third section is for the bevel, and this can be added or removed as desired. Additionally, this can be adjusted to achieve the desired bevel depth
Counter-Rotating Spindles
The left and right spindles are counter-rotating and are designed for climbing cuts, producing an optimum finish
Anti-Tear Out Blocks
On the fence side, there are independent phenolic tear-out blocks on both the tongue and groove sides. When the heads are set up, you machine the tear-out blocks to match your profile. This will ensure the material does not tear out on the fence side
Powerful 10HP Cutterhead Motors
Each cutterhead spindle is driven by an independent 10HP motor. The cross-cutting speed is infinitely adjustable to achieve the optimum finish quality on your end match
Feed System, Infeed, and Outfeed Clamps
The machine is equipped with (5) driven top rollers. The rollers are covered with urethane to provide optimum grip. Under the table, there are opposed idle feed wheels that are spring-loaded.
Adjustable Work Piece Clamping Unit
There are independent infeed and outfeed clamping units. These can be adjusted to accommodate widths up to 12" and various thicknesses up to 1.38".
Feed System (with the hood removed) and Dust Hood
The feed system is driven by a 1HP motor which drives a line shaft to the (5) feed rollers. The feed speed is infinitely adjustable through the touch screen
87″ Outfeed Slide Table
After the material has been processed, it comes out onto a ledge on the slide table. After it fully exits the machine, it will slide down onto the accumulation table and out of the way of the next board being processed
Tongue and Groove with Bevel Flooring or Paneling
The tong and groove can be adjusted to closely match the profile on your flooring or panelling. The bevel can be added or removed as desired
Capacity Width | 1.6" - 12" |
Capacity Thickness | .4" - 1.38" |
Minimum Length | 12" |
Maximum Length | Unlimited |
Feed Speed Maximum | 295 FPM |
Cutting Speed | 77 FPM |
Standard Powered Infeed Table | 173" |
Standard Outfeed Table | 86.6" |
Cutterheads | 10Hp x 2 |
Feed System | 1Hp |
Cutter Drive | 1/2 Hp |
Power | 460/3/60 |
Control Voltage | 24 VDC |
Connected Load | 21.5 HP |
Full Load Amperage | 25.20 Amps |
Clamping | Top and Side |
Spindle Diameter | 40mm |
Dust Collection Outlet | 6" Diameter |
Compressed Air Requirements | 85PSI appros. 12 CFM |
Please be advised that product(s) you’re purchasing may have State of California Prop 65 warnings associated. For more information, go to www.P65Warnings.ca.gov
Downloads
Specifications
Box Quantity | 1 |
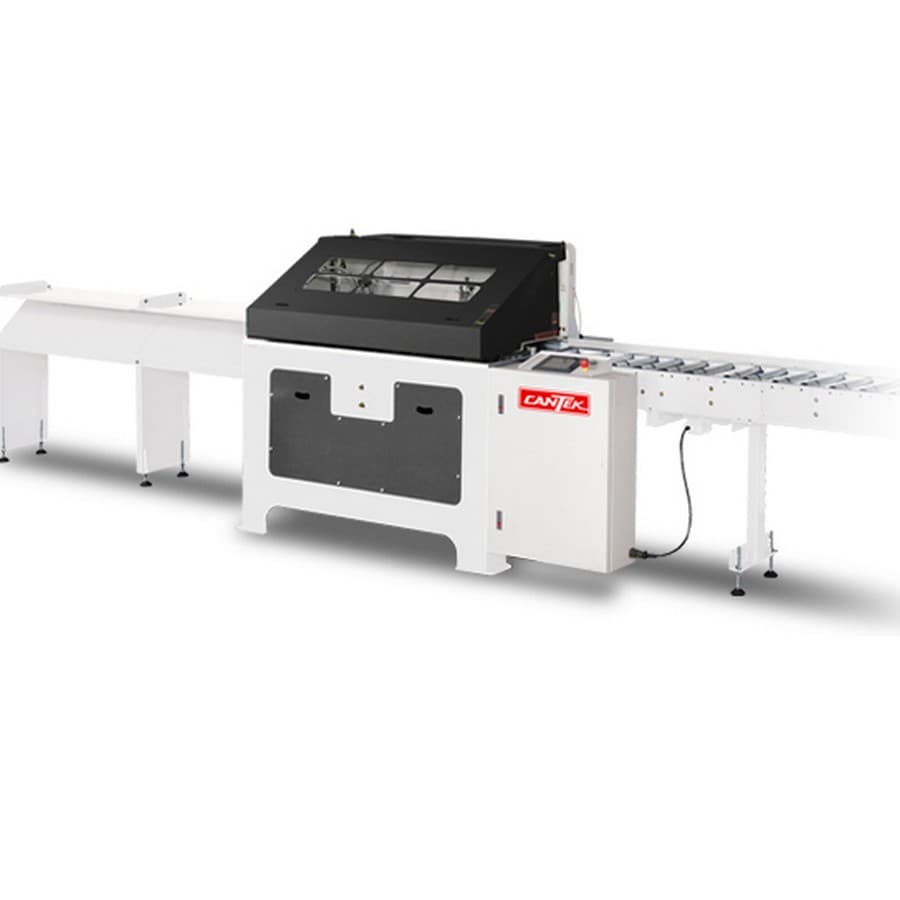
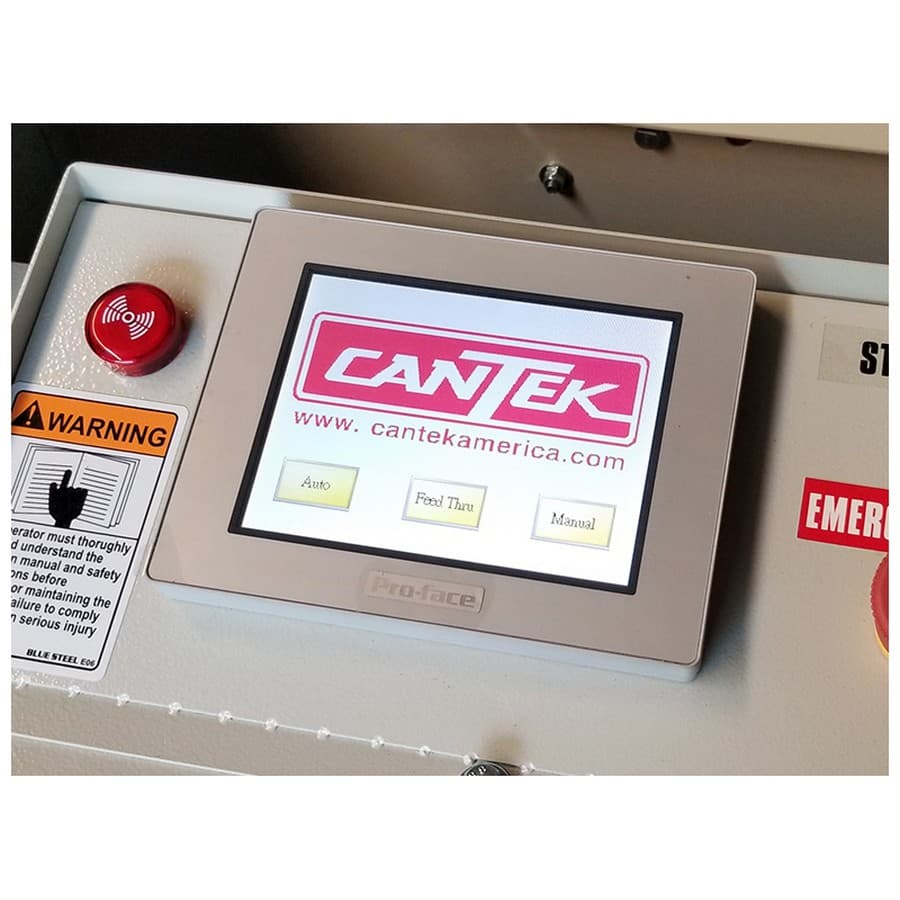
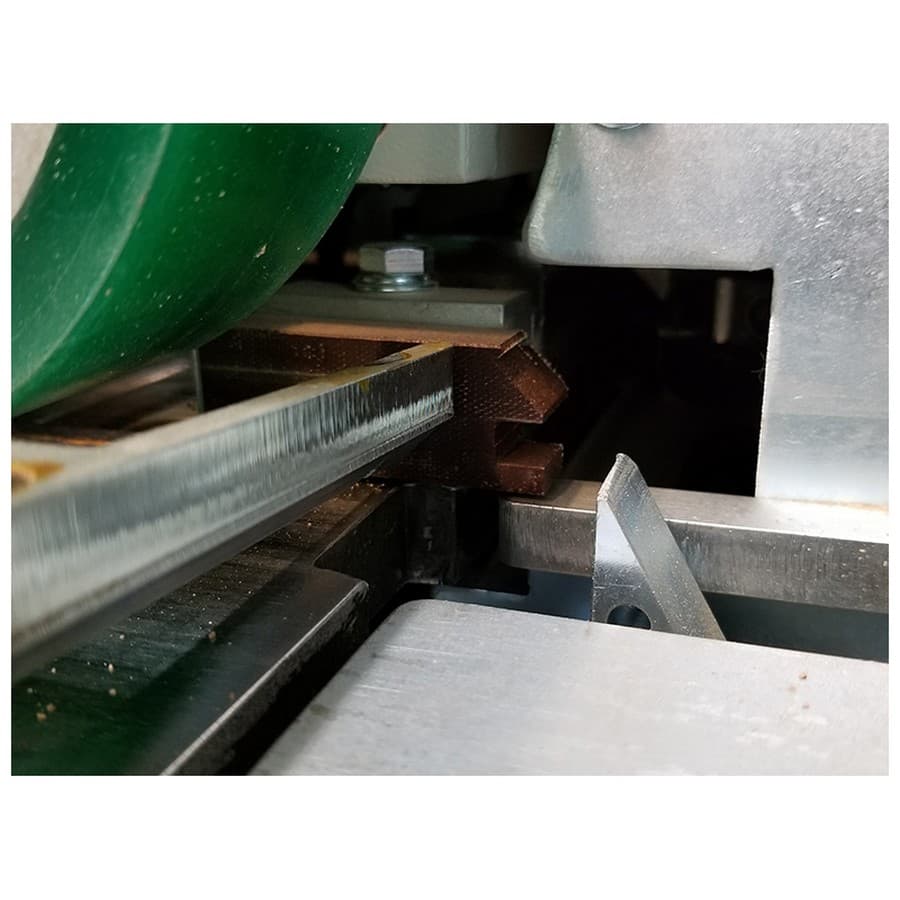
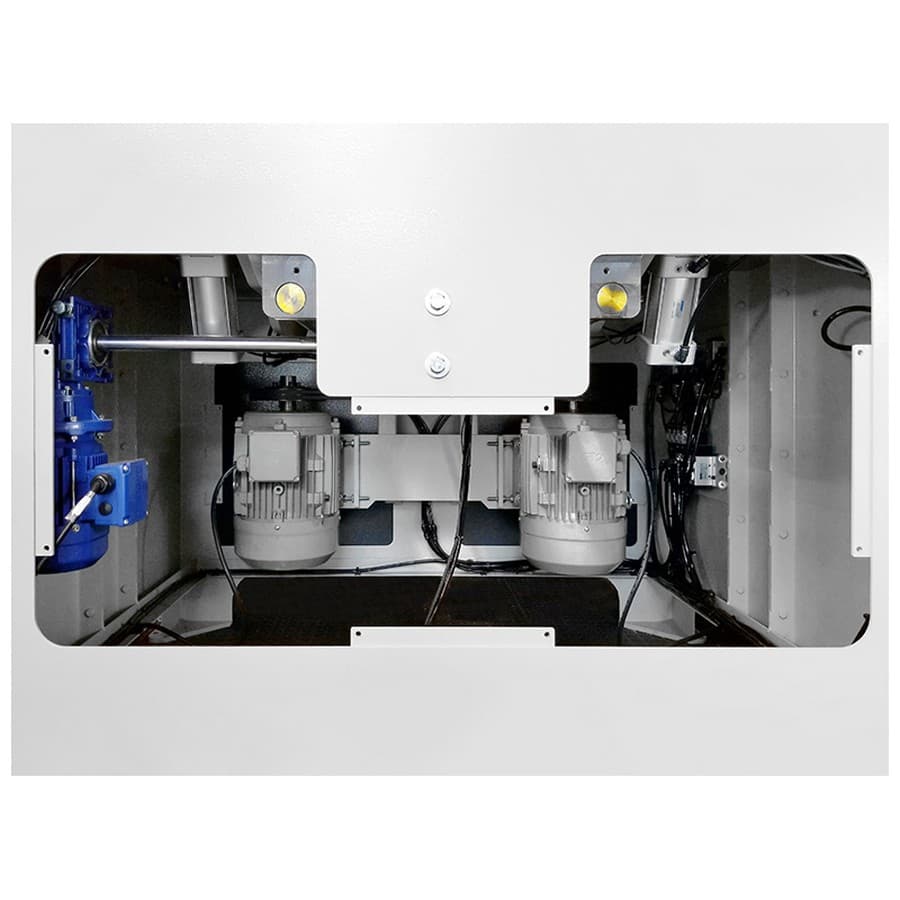
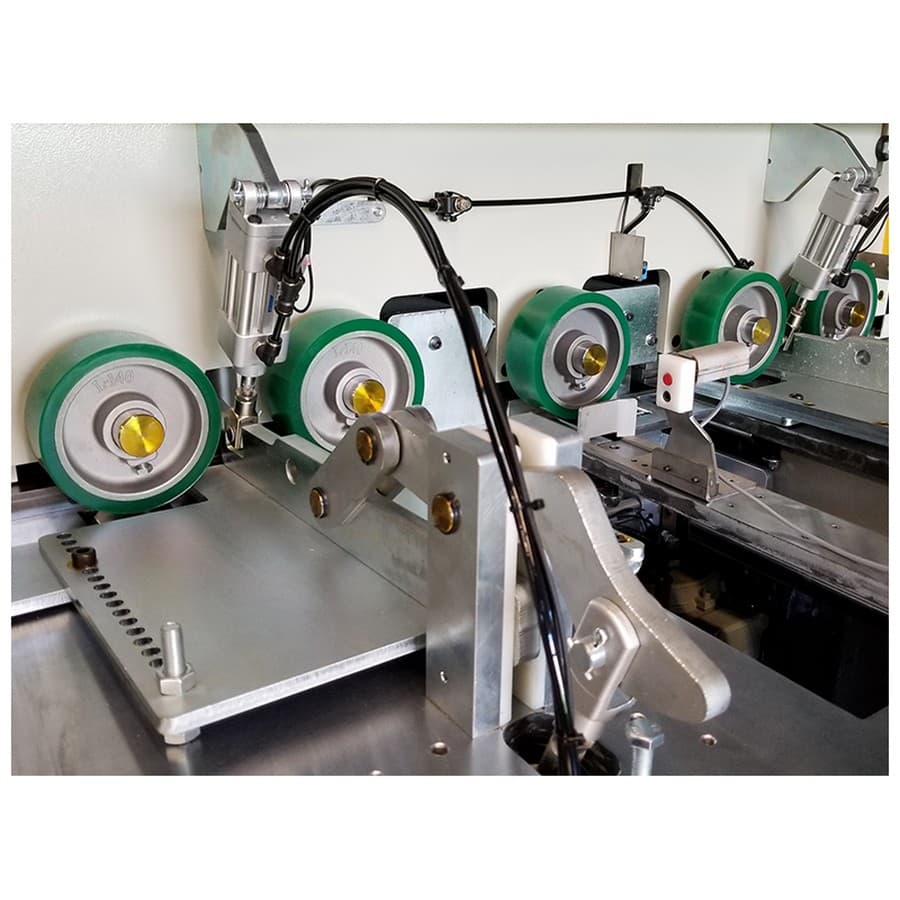
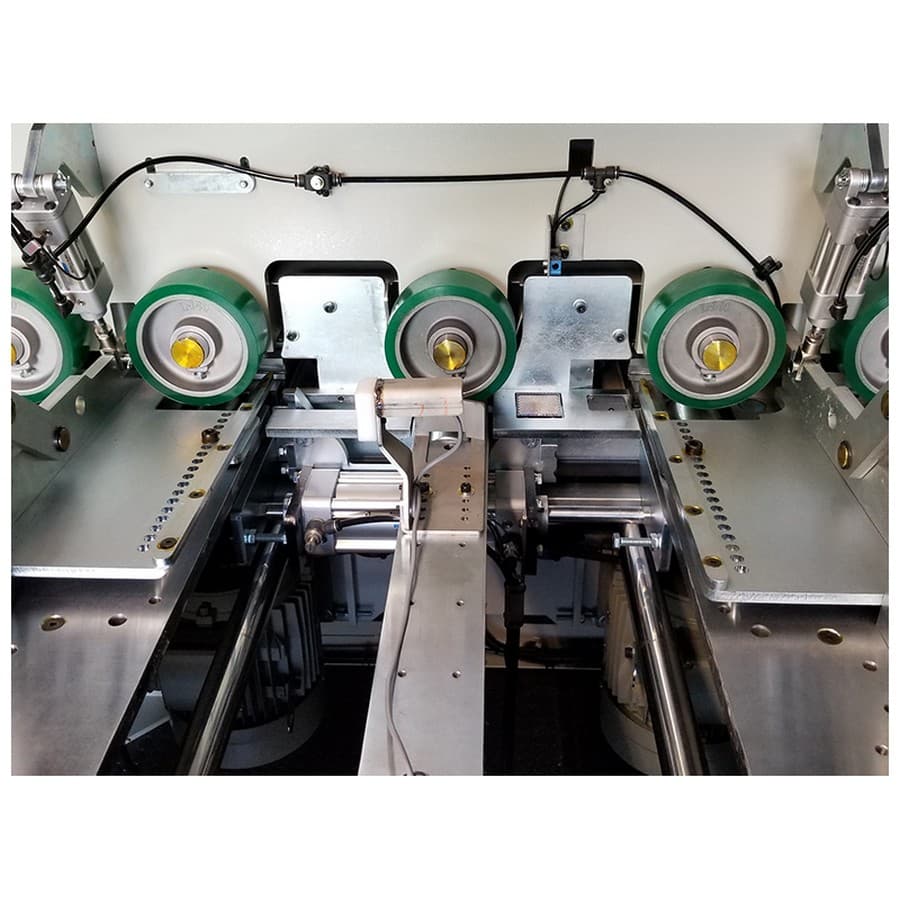
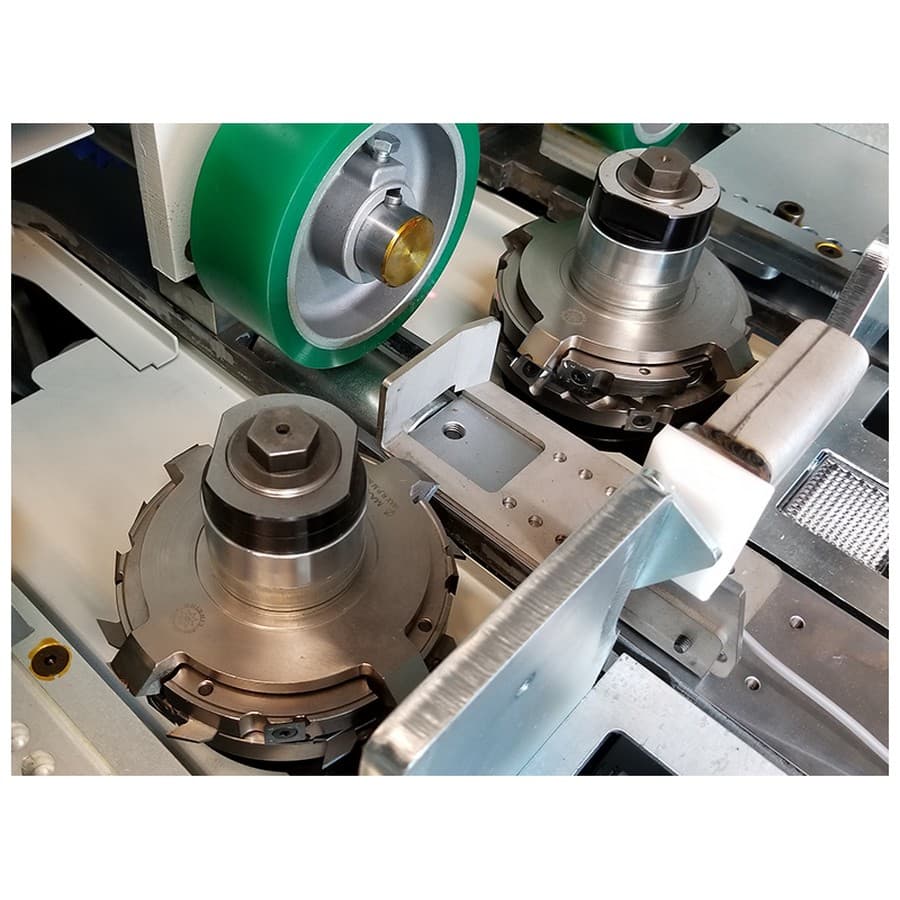
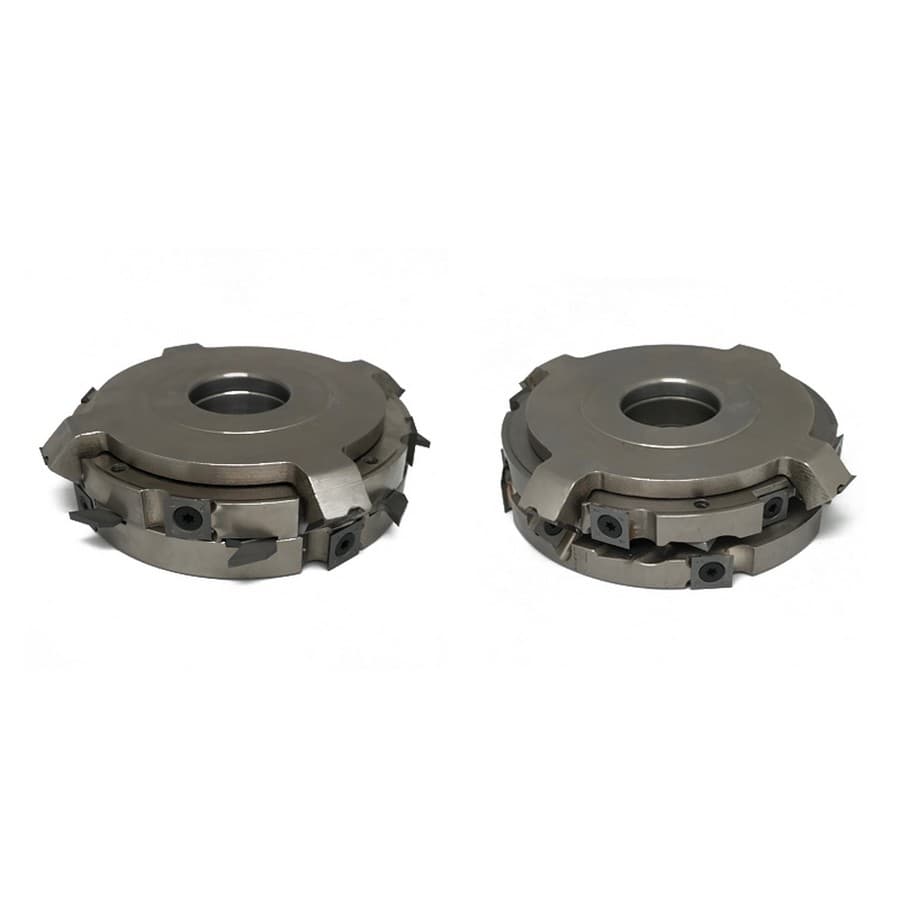
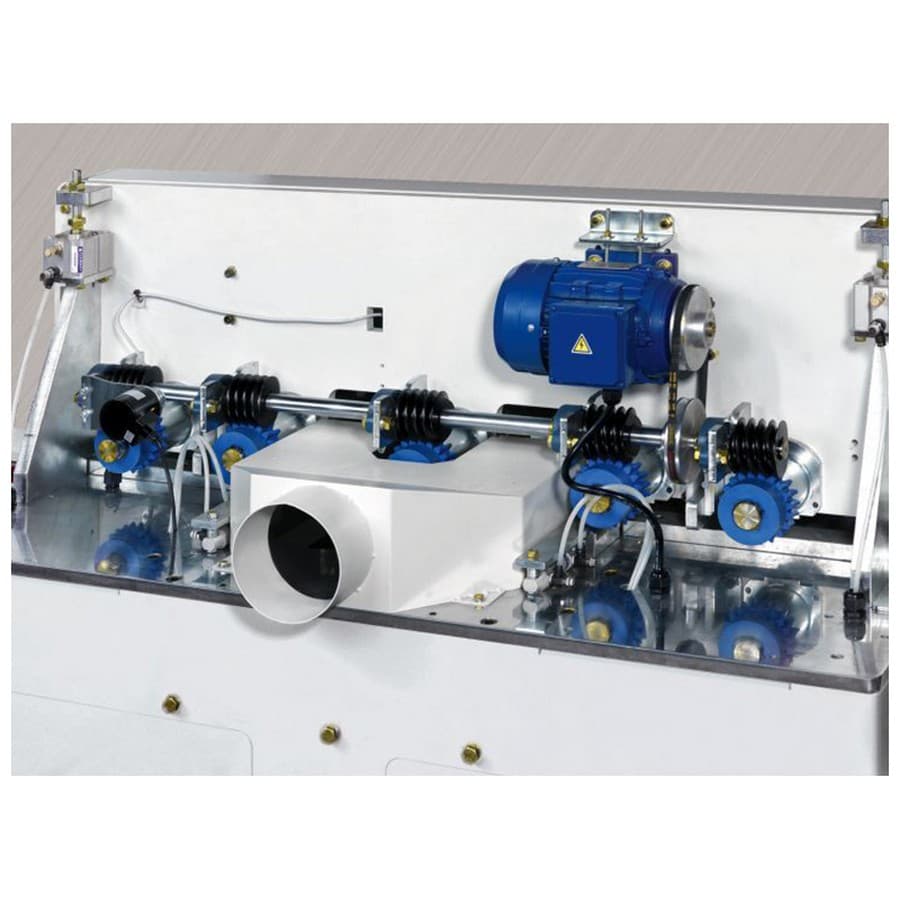

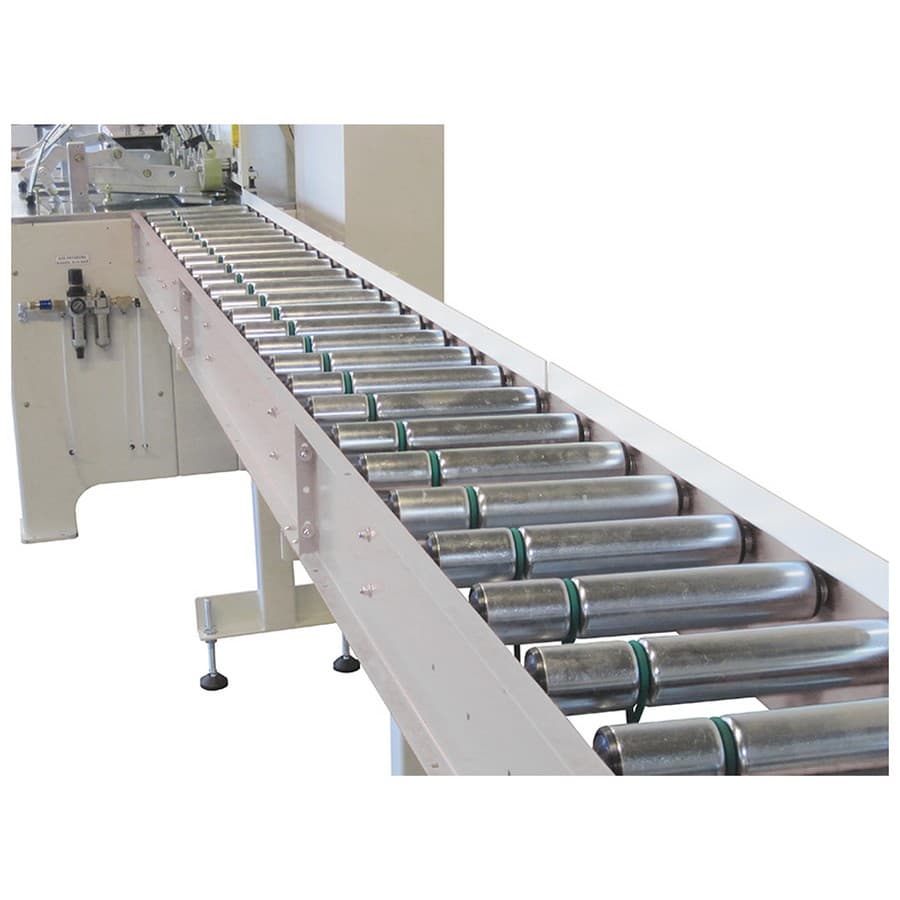
This item may incur additional shipping costs and lead times.
Product Details
The Cantek EM12 End Matcher is specially designed for machining tongue and groove (with or without bevels) on hardwood flooring and wall/ceiling paneling up to 12” wide. Its compact design with continuous through feed system allows for maximum output in a small space. Equipped with a user-friendly touch screen interface allow for simple operation with excellent performance and error diagnostics. The dual counter-rotating cutterheads produce both the tongue and groove simultaneously ensuring a perfect match. The anti-tear-out blocks and counter rotation of the heads ensure optimum cut quality without chipping or blowout. The insert style segmented cutterheads can be adjusted according to your desired tongue / groove thickness and can perform a micro-bevel or not. The variable speed infeed conveyor, variable feed speed, and variable cross-cutting speed allow the operator full control according to the type and size of material being run. The innovative clamps allow for simultaneous top and side clamping to ensure pieces are perfectly square for consistent end matching results.
Why Cantek EM12 End Matcher?
- Capable of processing end matching on flooring or paneling up to 12" wide x 1.38" thick.
- The Through-feed system allows the tongue and groove to be cut simultaneously on the tail of one board and the leading edge of the next board.
- Powerful dual 10HP cutterhead motors allow maximum cutting rate no matter the wood's width, thickness, or species.
- Stackable insert knife cutterheads allow for perfect matching of tongue and groove thickness.
- Variable cross-cutting feed speed and anti-tear-out blocks produce optimum finish quality on tongue and groove.
- Minimal floor space required with through feed design.
- A user-friendly PLC control touch screen can keep track of total linear feet cut as well as piece count.
- Production capacity of 77 lineal feet per minute based on an average of 6.5' board.
Key Advantages
- Variable speed through-feed system is controlled by frequency inverter.
- Powered top urethane rolls and spring-loaded bed rollers feed the material into position for processing.
- Pneumatic side pressure system ensures the material is held square against the fence.
- Capable of processing material as short as 12" to an unlimited length.
- Cutterheads are stacked and fully adjustable with replaceable and rotatable insert knives.
- Cutterheads are equipped with a removable micro-bevel insert cutter section for bevel or square flooring/paneling.
- 118" powered infeed table with angled rolls ensure material is fed up against the infeed fence.
- 87" outfeed slide table allows the board to slide out of the way while the next board comes through to be processed, resulting in continuous production.
- Chrome table ensures maximum wear resistance.
- Complete safety and noise reduction enclosure.
- The added feature of an inverter-controlled infeed conveyor allows you to slow the infeed speed when dealing with heavy boards.
Full Machine View & General Operation
The material travels from right to left. Each board is placed on the powered infeed conveyor and transferred automatically into the machine. The material will then be clamped and process the tongue on the right side and then groove on the left side. The material will exit the machine on the left and go on to a sliding table.
User-Friendly Touch Screen Control
The touch screen interface was designed with the operator in mind. It controls the machine's operation and keeps track of the number of pieces machined, total length machined, and more. These totals can be reset for each job if desired. Here you can also adjust the feed speed cutting speed of the machine.
118″ Powered Infeed Conveyor
The powered infeed conveyor brings material into the machine automatically. The rolls are slightly angled to bring material up against the fence. An inverter from the control panel adjusts the infeed conveyor speed to allow the operator to adjust the speed if necessary. For example, they may slow down the conveyor when feeding wide and long boards
Tongue and Groove Insert Knife Cutterheads
The tongue and groove cutters use insert knives that can be rotated for a fresh cutting edge. The cutterheads come in three sections which allows you to adjust the thickness of the groove and tongue. The third section is for the bevel, and this can be added or removed as desired. Additionally, this can be adjusted to achieve the desired bevel depth
Counter-Rotating Spindles
The left and right spindles are counter-rotating and are designed for climbing cuts, producing an optimum finish
Anti-Tear Out Blocks
On the fence side, there are independent phenolic tear-out blocks on both the tongue and groove sides. When the heads are set up, you machine the tear-out blocks to match your profile. This will ensure the material does not tear out on the fence side
Powerful 10HP Cutterhead Motors
Each cutterhead spindle is driven by an independent 10HP motor. The cross-cutting speed is infinitely adjustable to achieve the optimum finish quality on your end match
Feed System, Infeed, and Outfeed Clamps
The machine is equipped with (5) driven top rollers. The rollers are covered with urethane to provide optimum grip. Under the table, there are opposed idle feed wheels that are spring-loaded.
Adjustable Work Piece Clamping Unit
There are independent infeed and outfeed clamping units. These can be adjusted to accommodate widths up to 12" and various thicknesses up to 1.38".
Feed System (with the hood removed) and Dust Hood
The feed system is driven by a 1HP motor which drives a line shaft to the (5) feed rollers. The feed speed is infinitely adjustable through the touch screen
87″ Outfeed Slide Table
After the material has been processed, it comes out onto a ledge on the slide table. After it fully exits the machine, it will slide down onto the accumulation table and out of the way of the next board being processed
Tongue and Groove with Bevel Flooring or Paneling
The tong and groove can be adjusted to closely match the profile on your flooring or panelling. The bevel can be added or removed as desired
Capacity Width | 1.6" - 12" |
Capacity Thickness | .4" - 1.38" |
Minimum Length | 12" |
Maximum Length | Unlimited |
Feed Speed Maximum | 295 FPM |
Cutting Speed | 77 FPM |
Standard Powered Infeed Table | 173" |
Standard Outfeed Table | 86.6" |
Cutterheads | 10Hp x 2 |
Feed System | 1Hp |
Cutter Drive | 1/2 Hp |
Power | 460/3/60 |
Control Voltage | 24 VDC |
Connected Load | 21.5 HP |
Full Load Amperage | 25.20 Amps |
Clamping | Top and Side |
Spindle Diameter | 40mm |
Dust Collection Outlet | 6" Diameter |
Compressed Air Requirements | 85PSI appros. 12 CFM |
Please be advised that product(s) you’re purchasing may have State of California Prop 65 warnings associated. For more information, go to www.P65Warnings.ca.gov
Downloads
Specifications
Box Quantity | 1 |