Morbidelli N100 22 CR Belt 7 X 10 CNC Machining Center
This item may incur additional shipping costs and lead times.
Product Details
The Morbidelli N100 owes its rigidity to the design and weight of its reinforced base and innovative one-piece frame. All portions of the base are of heavy gauge steel and are normalized after welding, a process which ensures that all stress in the base is removed before it is machined and drilled for the guides.
Today's machining centers are being asked to perform a wide variety of operations at the highest speeds possible while, at the same time, maintaining a high quality of cut. Micro-vibrations are created around all types of CNC machining centers where there is head positioning, drilling, and high-speed routing taking place on the machine base. SCM solves the problem of deadening vibration as well as offering rigidity by employing heavy gauge steel members for the base of the machine. This weight coupled with the one-piece frame offers the best combination of rigidity and balanced strength on a bridge design. Movement along the X &Y is high precision rack and pinion while the Z-axes is driven by a ball screw.
High Precision, High Load Prismatic Bearing Guides
SCM uses prismatic guides for support in all axes. Due to their added weight load capability (approximately 4 times that of conventional round guides), prismatic type guides can permit accurate head positioning at high speeds.
A.C. Servo Motors X, Y & Z Axes
A.C. servomotors, or A.C. brushless motors as they are sometimes called, are the latest in electronic linear motion technology. A.C. servomotors use less power and produce a more even output (drive) throughout the power band. The ability to maintain a constant torque setting when going from an idle setting into a heavy rout produces cleaner cuts and longer tool life. These motors are controlled by digital supply cards that offer the reliability and precision fine tuning associated with solid state electronics.
Solid State Inverter Controls Router RPM
Solid State frequency inverters support the programmable router spindle speeds (S functions). By utilizing digital inverter technology, the programmer can select the correct cutter RPM and match it to the correct linear/rotational feed speed for the specific application and/or material being cut. This will give optimum quality of cut while greatly extending tool life. The inverter also acts as an electronic brake, stopping the router spindle motor in microseconds if an emergency signal is given.
PRO-SPACE Safety System
The absence of fences surrounding the machine allows the operator easily access the working table from any position around the machine with no need to wait for the program interruption. The maximum speed of the axes is limited by the software to 25 m/min (984 in/min), fulfilling current safety norms. This arrangement grants the operator to work in total safety.
The Pro-Space system allows the machine to take a small sized footprint. Thanks to the exclusive solution of integrating the electrical cabinet and the vacuum pump inside the frame structure, SCM has the ability to install the machine even in the smallest shops while avoiding repositioning of any equipment.
Electrical Connection with Voltage Different than 380/400V - 50/60Hz
The machine is equipped with an autotransformer to convert the voltage coming from the main electrical supply to the voltage required to make the machine operative. Instructions for correct electrical connections to the customer power grid are included in the document 90L0635760A which is provided with the machine.
The transformer/auto transformer is ALWAYS:
1) NOT regarded as part of the standard machine supply, but must be integrated in the electrical equipment of the customer’s company
2) NOT connected to the machine by the manufacturer
3) Connected and checked BY THE CUSTOMER
• The autotransformer includes the connection of the neutral for generating 220V inside the electric panel
Allowed electricity supply networks: TN-S / TN-C
Electric Cabinet with Air Conditioning Device
It maintains temperature of approx. 18°C inside the electric cabinet. This option is advisable in environment with temperatures over 35°C.
"HE" High Performance Aluminium Multifunction Worktable
High-capacity aluminum table, with dual vacuum areas has an answer to most component nesting scenarios. The Vacuum holes set at 120 mm pitch, closure by means of rapid magnetic system “patent pending”. Grooves are set at 20mm from each other for fixing of the workpiece using rubbers seals.
In addition to nesting full sheets, the Morbidelli N100 can also be used for routing smaller components. For work on the face of the component, rubber gasket material can be used to isolate the vacuum for part hold-down. This eliminates the need for special fixturing devices as is necessary on many machines. When machining the edges of parts, the patented MODULSET system raises the component so work can take place without damage to the worktable.
The magnetic system for opening and closing the vacuum passages allows for an extremely quick table set up when the vacuum is only required in a portion of the table. With a dedicated tool (supplied) it is a matter of seconds to perform the set up with no need for a screwdriver.
Left rear stops for "A" field
Moving pins must be approved by the Service Department and may have additional costs.
This code includes:
• Vacuum area for half or entire working area
• It allows to convey all vacuum on half working area (left or right) or on the entire working area (left and right)
• Alternated work process: It allows to lock a workpiece on a side when machining on the opposite one
Retractable Stops for “E” and “H” Fields Managed by NC
No. 3 front stops and no. 1 left lateral stop for E field, no. 3 front stops and no. 1 right lateral stop for H field. Total 8 stops. Does not include installation cost.
Hiteco Electrospindle 9.5kW (13HP)
It includes:
• HSK F 63 quick release tool-holder
• 1,500 – 24,000rpm spindle speed
• (S1/S6) 8/9.5 kW (11/13 HP) constant motor power from 12,000 to 18,000rpm
• right and left rotation
• static inverter for continuous speed and rapid shutdown of rotation
• exhaust hood around whole perimeter
Notes:
Tool-holders and expansible collets are not included.
Pre-arrangement for "Hiteco" Aggregates
It allows the angular driven heads fitting on electrospindle, with fixed mechanical
coupling with reference pin.
Air blowers on the Electrospindle
No.4 air blowers capable to convey the chips produced by the cutter during machining. This facilitates the chip ejection.
F12 Drill Head
This drilling unit includes:
• twelve (12) independent vertical spindles (7 right and 5 left)
• attachment for vertical and horizontal bits: 10 mm diameter
• center-to-center distance between spindles: 32 mm
• bits rotation speed: 4,200 rpm
• bits rotation speed with inverter: 8,000 rpm max.
• 2.2 kW motor power
• vertical ON/OFF stroke of each spindle: 60 mm
Drilling Unit Managed by Inverter
It allows the rotating speed programming up to 8000 rpm maximum for the drilling bits and 10000 rpm for the blade.
Notes:
The passage between routing and boring and vice versa, implies to wait for the motor stop.
TR 13 Position Tool Changer- Higher Capacity with 19 Positions
Side tool holder with reduced inter axis, in order to accommodate a higher number of tools. Furthermore, this code includes the exhaust hood with on-off automatic positioning and manual adjustment on 4 different positions. The new available places of the tool-holders are the following: TR13 increased to 19 places.
• Maximum number of tools that can be installed: 19
• Tool attachment: HSK 63F
Management of Long Tools
Machine equipment to install heads for non-wood applications
• Three (3) places maximum
• Maximum groups length, 200mm tools included
Tool Touch Probe
Electronic system positioned on the base side which allows for detecting tool length without running a test program.
One (1) 300 Cubic Meter/Hour Vacuum Pump
The vacuum hold-down system features a 300 cubic meter/hour vacuum pump. It offers the reliability of a substantial increase in vacuum power and allows the use of spoil boards for nesting full sheets. Optional additional vacuum pump must be external to the machine base.
Additional 300 Cubic Meter/Hour Vacuum Pump
An additional 300m3/h pump is placed for added vacuum hold-down capability.
Ventilation System on Machine Base
It is particularly suitable for hot climates and for the use of materials sensitive to the heat; this ventilation system and base insulation ensure a low temperature of the working table.
Automatic Lube
The correct grease level on the machine moving parts is always maintained by means of an electronic control (X, Y, Z axis)
Remote “TECPAD” Pendant
The 7” COLOR display allows for the effective management of all machine functions from movement of controlled axes in Manual Jog Mode to loading and execution of a program. The unit is also fitted with a USB Port, which allows for a quick load and setup of new programs.
Console with Integrated PC "Eye-M PRO"
Device connected to the CNC machine which allows the usage of the supplied software. The integrated LED light bar allows the operator to check in real time the state of the machine (emergency, operative, etc.) without the need to be on the console itself.
It is equipped with an iPC with "fanless" construction and IP53 grade protection (IP65 on the front side). This robust solution grants the highest durability even in the worst environmental conditions which an industrial site may present.
The 21.5" LCD color display through a 16/9 sized touch screen grants an unbeatable easiness and efficiency in controlling the main functions of the machine, also through:
• Full HD display resolution 1920x1080
• LED lighting
• Multi-touch screen – 10 points of contact
• Wide visual angle 176° Horizontal / 160° Vertical
• "Zero Pixel Defect" quality
• Intel i7 – 2,9-3,8 Ghz
• RAM 8GB – DDR4
• Hard disk: 256GB SSD
• O.S. Windows Embedded Standard 10 IoT- 64bit
• QWERTY keyboard with English layout
• Wired mouse – 3 functions
• Ethernet port RJ45
• USB port 3.0 protocol supported
• Nominal operating temperature: +5°C / +35°C
Automatic Unloading System
The N100 15 CR can be equipped with an outfeed pusher on the left side. The automatic workpiece pusher is connected to the machine’s movement in the X axis. It can push the components with up to a total weight of 200kg (440lbs.). Furthermore, it is equipped with an exhaust system that automatically cleans the spoil board during the unloading phase. Automatic adjustment of the pusher height though a lining on the support panel (included in the machine supply)
• Top Exhaust outlet diameter: 300 mm (Oval)
• Bottom Exhaust outlet diameter: 200 mm
• Exhaust air speed: 30 mt/sec
• Exhaust air consumption: 3400 m3/h
• It can push the workpieces up to a total weight of:
• Morbidelli n100 12 = Kg 150 (330lbs)
• Morbidelli n100 15/S18/S22-31 = Kg 200 (440lbs)
• Morbidelli n100 22-43 = Kg 300 (660lbs)
• Maximum thickness (spoil board included): 40 mm
Outfeed Conveyor Belt Located on Left Side
Powered belt capable to move the workpieces from the machine table, up to the unloading position. This position is equipped with photocell automatic detecting system for the belt start/stop and pushbutton for the belt manual speed. Installation included if done at when machine is installed.
Specifications
Box Quantity | 1 |
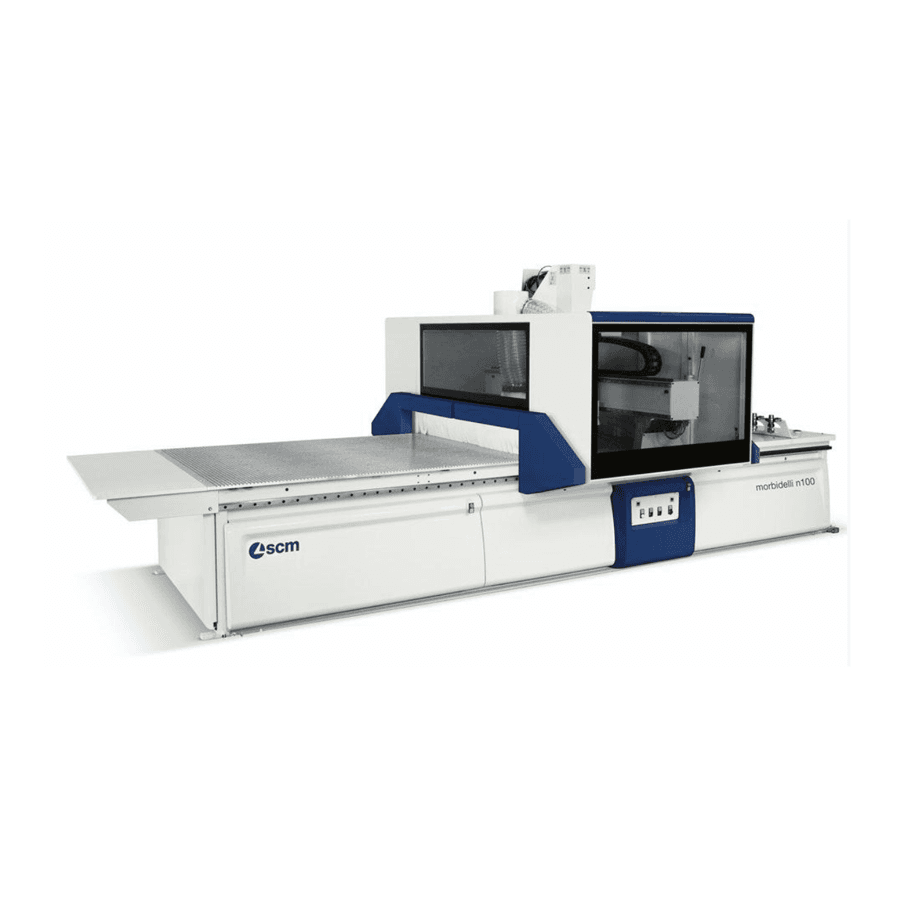
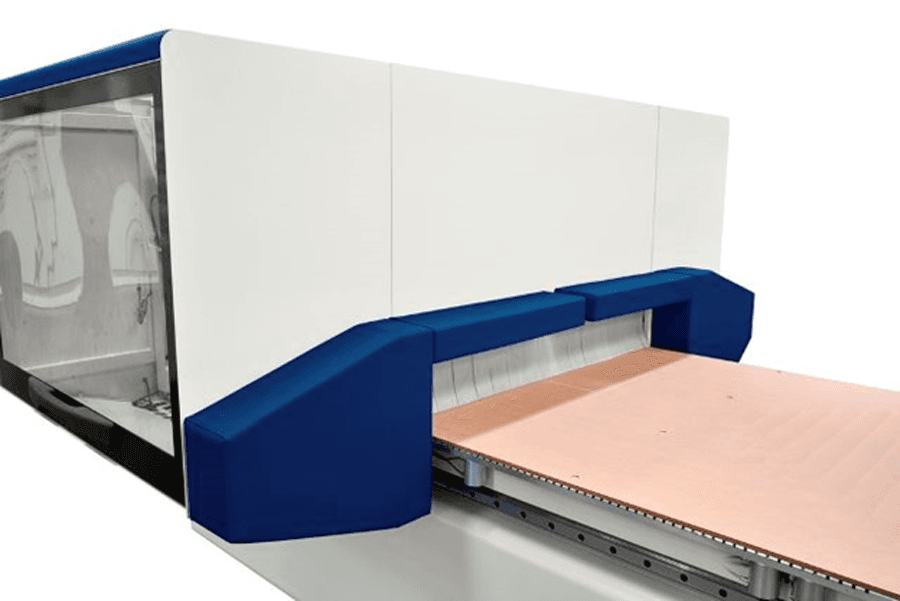
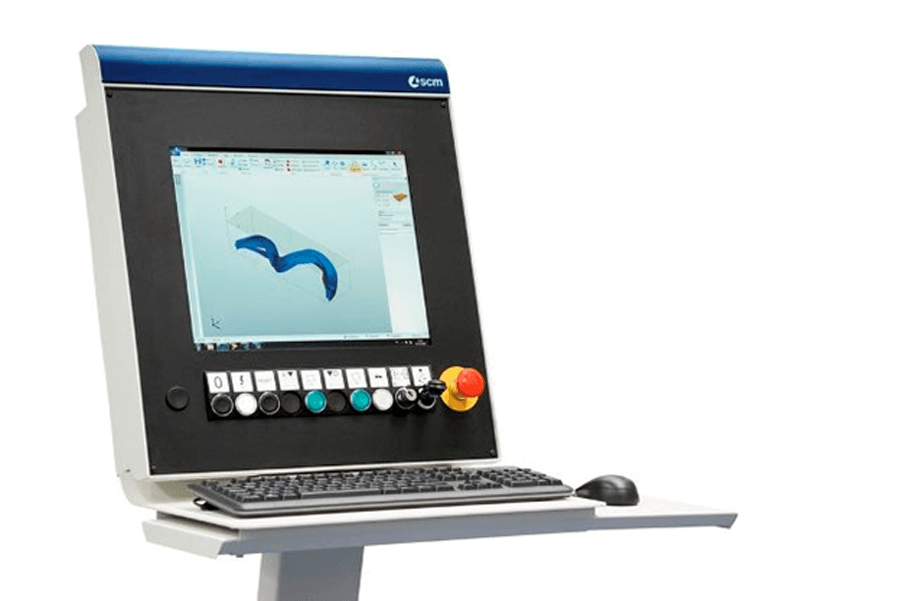
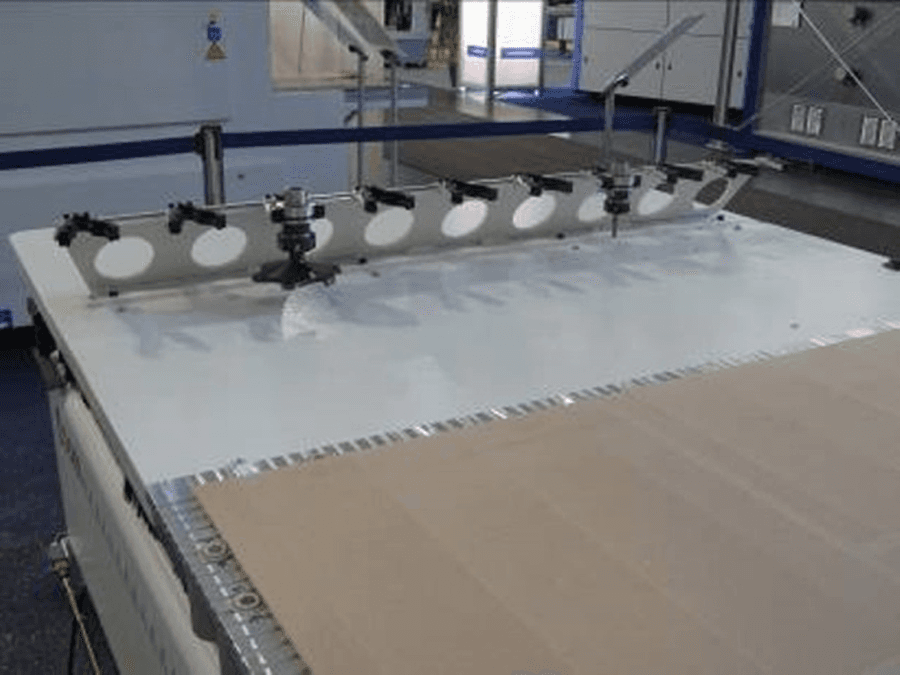
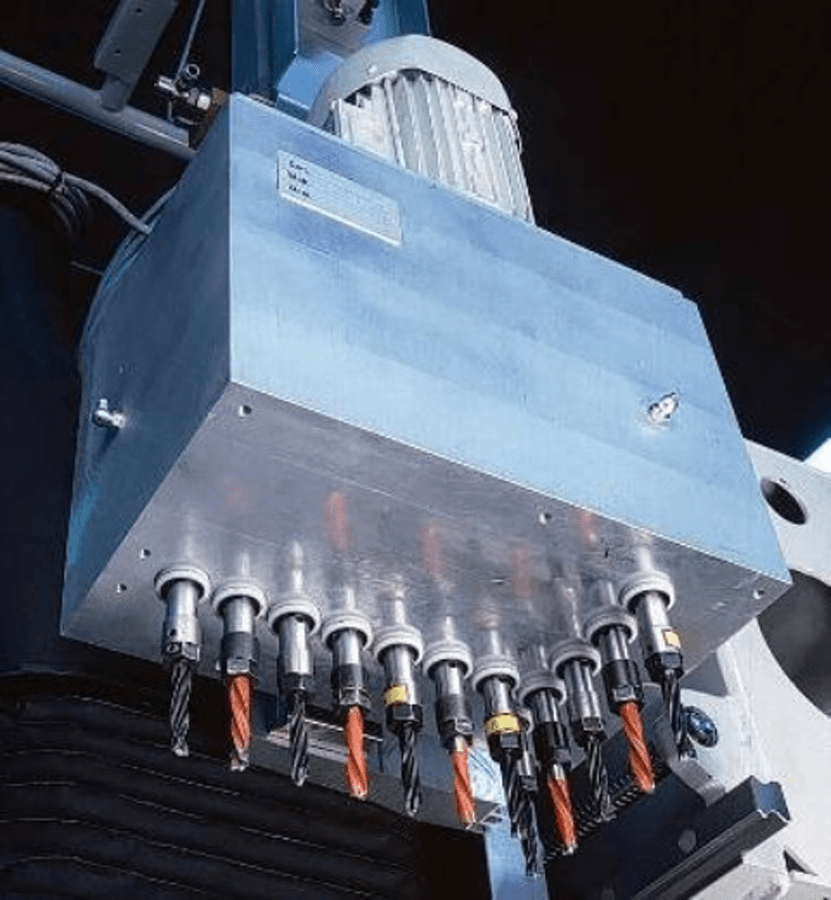
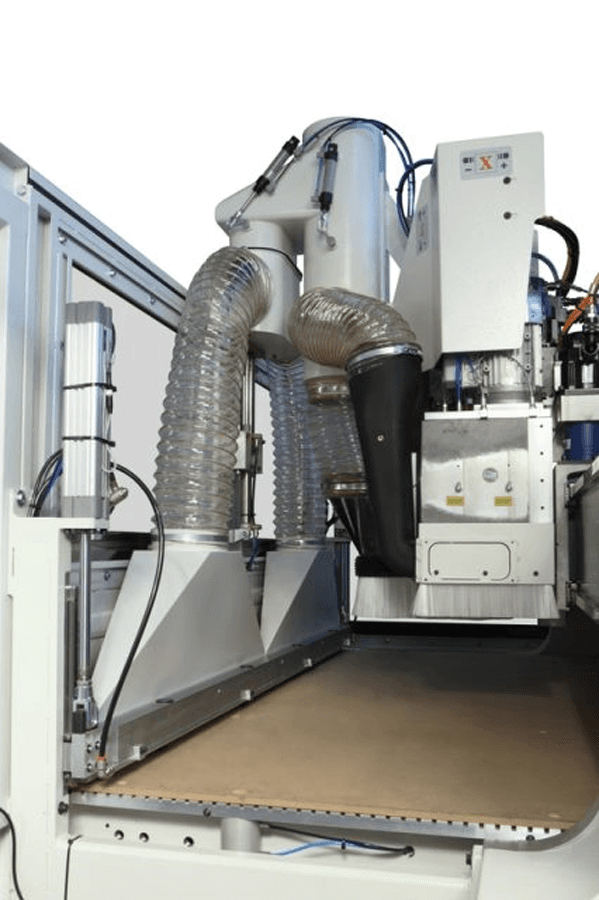
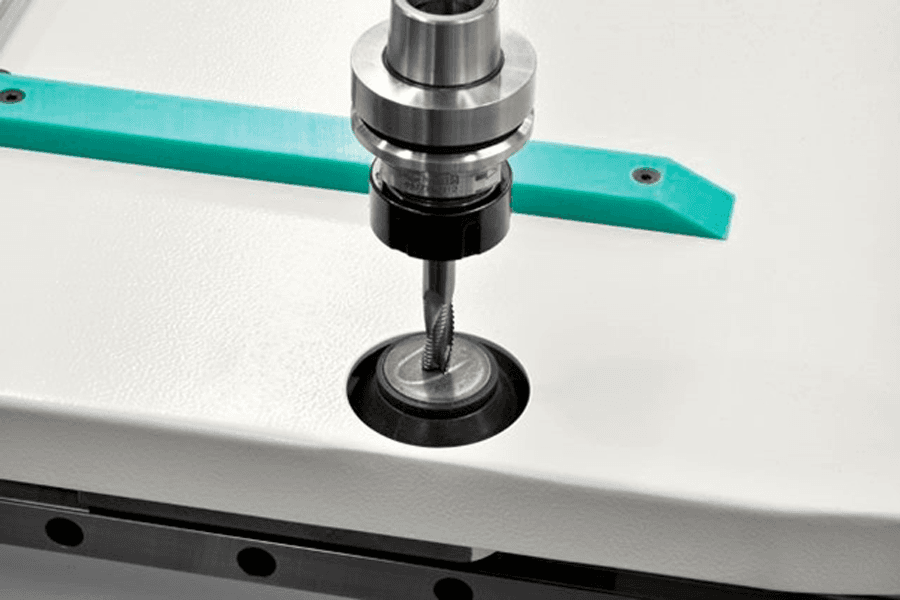
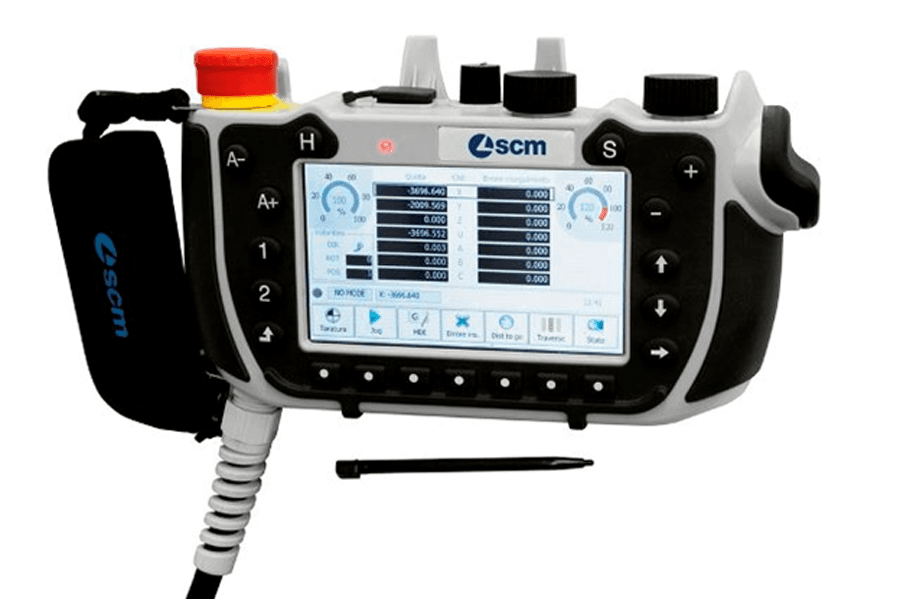
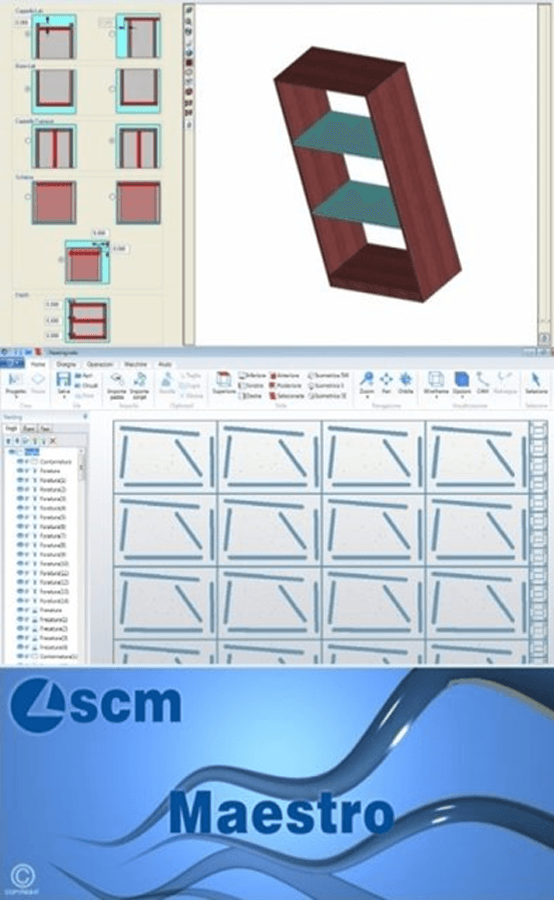
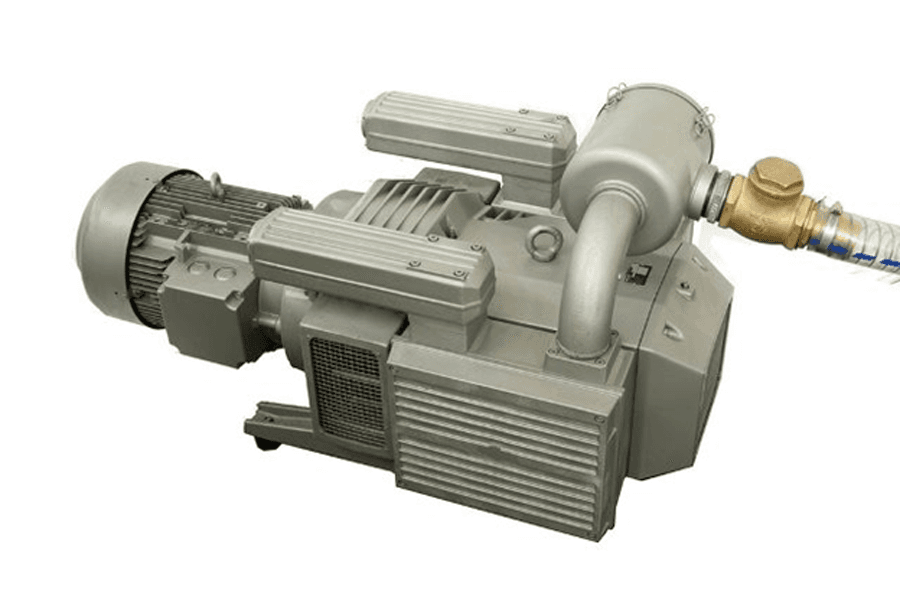
This item may incur additional shipping costs and lead times.
Product Details
The Morbidelli N100 owes its rigidity to the design and weight of its reinforced base and innovative one-piece frame. All portions of the base are of heavy gauge steel and are normalized after welding, a process which ensures that all stress in the base is removed before it is machined and drilled for the guides.
Today's machining centers are being asked to perform a wide variety of operations at the highest speeds possible while, at the same time, maintaining a high quality of cut. Micro-vibrations are created around all types of CNC machining centers where there is head positioning, drilling, and high-speed routing taking place on the machine base. SCM solves the problem of deadening vibration as well as offering rigidity by employing heavy gauge steel members for the base of the machine. This weight coupled with the one-piece frame offers the best combination of rigidity and balanced strength on a bridge design. Movement along the X &Y is high precision rack and pinion while the Z-axes is driven by a ball screw.
High Precision, High Load Prismatic Bearing Guides
SCM uses prismatic guides for support in all axes. Due to their added weight load capability (approximately 4 times that of conventional round guides), prismatic type guides can permit accurate head positioning at high speeds.
A.C. Servo Motors X, Y & Z Axes
A.C. servomotors, or A.C. brushless motors as they are sometimes called, are the latest in electronic linear motion technology. A.C. servomotors use less power and produce a more even output (drive) throughout the power band. The ability to maintain a constant torque setting when going from an idle setting into a heavy rout produces cleaner cuts and longer tool life. These motors are controlled by digital supply cards that offer the reliability and precision fine tuning associated with solid state electronics.
Solid State Inverter Controls Router RPM
Solid State frequency inverters support the programmable router spindle speeds (S functions). By utilizing digital inverter technology, the programmer can select the correct cutter RPM and match it to the correct linear/rotational feed speed for the specific application and/or material being cut. This will give optimum quality of cut while greatly extending tool life. The inverter also acts as an electronic brake, stopping the router spindle motor in microseconds if an emergency signal is given.
PRO-SPACE Safety System
The absence of fences surrounding the machine allows the operator easily access the working table from any position around the machine with no need to wait for the program interruption. The maximum speed of the axes is limited by the software to 25 m/min (984 in/min), fulfilling current safety norms. This arrangement grants the operator to work in total safety.
The Pro-Space system allows the machine to take a small sized footprint. Thanks to the exclusive solution of integrating the electrical cabinet and the vacuum pump inside the frame structure, SCM has the ability to install the machine even in the smallest shops while avoiding repositioning of any equipment.
Electrical Connection with Voltage Different than 380/400V - 50/60Hz
The machine is equipped with an autotransformer to convert the voltage coming from the main electrical supply to the voltage required to make the machine operative. Instructions for correct electrical connections to the customer power grid are included in the document 90L0635760A which is provided with the machine.
The transformer/auto transformer is ALWAYS:
1) NOT regarded as part of the standard machine supply, but must be integrated in the electrical equipment of the customer’s company
2) NOT connected to the machine by the manufacturer
3) Connected and checked BY THE CUSTOMER
• The autotransformer includes the connection of the neutral for generating 220V inside the electric panel
Allowed electricity supply networks: TN-S / TN-C
Electric Cabinet with Air Conditioning Device
It maintains temperature of approx. 18°C inside the electric cabinet. This option is advisable in environment with temperatures over 35°C.
"HE" High Performance Aluminium Multifunction Worktable
High-capacity aluminum table, with dual vacuum areas has an answer to most component nesting scenarios. The Vacuum holes set at 120 mm pitch, closure by means of rapid magnetic system “patent pending”. Grooves are set at 20mm from each other for fixing of the workpiece using rubbers seals.
In addition to nesting full sheets, the Morbidelli N100 can also be used for routing smaller components. For work on the face of the component, rubber gasket material can be used to isolate the vacuum for part hold-down. This eliminates the need for special fixturing devices as is necessary on many machines. When machining the edges of parts, the patented MODULSET system raises the component so work can take place without damage to the worktable.
The magnetic system for opening and closing the vacuum passages allows for an extremely quick table set up when the vacuum is only required in a portion of the table. With a dedicated tool (supplied) it is a matter of seconds to perform the set up with no need for a screwdriver.
Left rear stops for "A" field
Moving pins must be approved by the Service Department and may have additional costs.
This code includes:
• Vacuum area for half or entire working area
• It allows to convey all vacuum on half working area (left or right) or on the entire working area (left and right)
• Alternated work process: It allows to lock a workpiece on a side when machining on the opposite one
Retractable Stops for “E” and “H” Fields Managed by NC
No. 3 front stops and no. 1 left lateral stop for E field, no. 3 front stops and no. 1 right lateral stop for H field. Total 8 stops. Does not include installation cost.
Hiteco Electrospindle 9.5kW (13HP)
It includes:
• HSK F 63 quick release tool-holder
• 1,500 – 24,000rpm spindle speed
• (S1/S6) 8/9.5 kW (11/13 HP) constant motor power from 12,000 to 18,000rpm
• right and left rotation
• static inverter for continuous speed and rapid shutdown of rotation
• exhaust hood around whole perimeter
Notes:
Tool-holders and expansible collets are not included.
Pre-arrangement for "Hiteco" Aggregates
It allows the angular driven heads fitting on electrospindle, with fixed mechanical
coupling with reference pin.
Air blowers on the Electrospindle
No.4 air blowers capable to convey the chips produced by the cutter during machining. This facilitates the chip ejection.
F12 Drill Head
This drilling unit includes:
• twelve (12) independent vertical spindles (7 right and 5 left)
• attachment for vertical and horizontal bits: 10 mm diameter
• center-to-center distance between spindles: 32 mm
• bits rotation speed: 4,200 rpm
• bits rotation speed with inverter: 8,000 rpm max.
• 2.2 kW motor power
• vertical ON/OFF stroke of each spindle: 60 mm
Drilling Unit Managed by Inverter
It allows the rotating speed programming up to 8000 rpm maximum for the drilling bits and 10000 rpm for the blade.
Notes:
The passage between routing and boring and vice versa, implies to wait for the motor stop.
TR 13 Position Tool Changer- Higher Capacity with 19 Positions
Side tool holder with reduced inter axis, in order to accommodate a higher number of tools. Furthermore, this code includes the exhaust hood with on-off automatic positioning and manual adjustment on 4 different positions. The new available places of the tool-holders are the following: TR13 increased to 19 places.
• Maximum number of tools that can be installed: 19
• Tool attachment: HSK 63F
Management of Long Tools
Machine equipment to install heads for non-wood applications
• Three (3) places maximum
• Maximum groups length, 200mm tools included
Tool Touch Probe
Electronic system positioned on the base side which allows for detecting tool length without running a test program.
One (1) 300 Cubic Meter/Hour Vacuum Pump
The vacuum hold-down system features a 300 cubic meter/hour vacuum pump. It offers the reliability of a substantial increase in vacuum power and allows the use of spoil boards for nesting full sheets. Optional additional vacuum pump must be external to the machine base.
Additional 300 Cubic Meter/Hour Vacuum Pump
An additional 300m3/h pump is placed for added vacuum hold-down capability.
Ventilation System on Machine Base
It is particularly suitable for hot climates and for the use of materials sensitive to the heat; this ventilation system and base insulation ensure a low temperature of the working table.
Automatic Lube
The correct grease level on the machine moving parts is always maintained by means of an electronic control (X, Y, Z axis)
Remote “TECPAD” Pendant
The 7” COLOR display allows for the effective management of all machine functions from movement of controlled axes in Manual Jog Mode to loading and execution of a program. The unit is also fitted with a USB Port, which allows for a quick load and setup of new programs.
Console with Integrated PC "Eye-M PRO"
Device connected to the CNC machine which allows the usage of the supplied software. The integrated LED light bar allows the operator to check in real time the state of the machine (emergency, operative, etc.) without the need to be on the console itself.
It is equipped with an iPC with "fanless" construction and IP53 grade protection (IP65 on the front side). This robust solution grants the highest durability even in the worst environmental conditions which an industrial site may present.
The 21.5" LCD color display through a 16/9 sized touch screen grants an unbeatable easiness and efficiency in controlling the main functions of the machine, also through:
• Full HD display resolution 1920x1080
• LED lighting
• Multi-touch screen – 10 points of contact
• Wide visual angle 176° Horizontal / 160° Vertical
• "Zero Pixel Defect" quality
• Intel i7 – 2,9-3,8 Ghz
• RAM 8GB – DDR4
• Hard disk: 256GB SSD
• O.S. Windows Embedded Standard 10 IoT- 64bit
• QWERTY keyboard with English layout
• Wired mouse – 3 functions
• Ethernet port RJ45
• USB port 3.0 protocol supported
• Nominal operating temperature: +5°C / +35°C
Automatic Unloading System
The N100 15 CR can be equipped with an outfeed pusher on the left side. The automatic workpiece pusher is connected to the machine’s movement in the X axis. It can push the components with up to a total weight of 200kg (440lbs.). Furthermore, it is equipped with an exhaust system that automatically cleans the spoil board during the unloading phase. Automatic adjustment of the pusher height though a lining on the support panel (included in the machine supply)
• Top Exhaust outlet diameter: 300 mm (Oval)
• Bottom Exhaust outlet diameter: 200 mm
• Exhaust air speed: 30 mt/sec
• Exhaust air consumption: 3400 m3/h
• It can push the workpieces up to a total weight of:
• Morbidelli n100 12 = Kg 150 (330lbs)
• Morbidelli n100 15/S18/S22-31 = Kg 200 (440lbs)
• Morbidelli n100 22-43 = Kg 300 (660lbs)
• Maximum thickness (spoil board included): 40 mm
Outfeed Conveyor Belt Located on Left Side
Powered belt capable to move the workpieces from the machine table, up to the unloading position. This position is equipped with photocell automatic detecting system for the belt start/stop and pushbutton for the belt manual speed. Installation included if done at when machine is installed.
Specifications
Box Quantity | 1 |